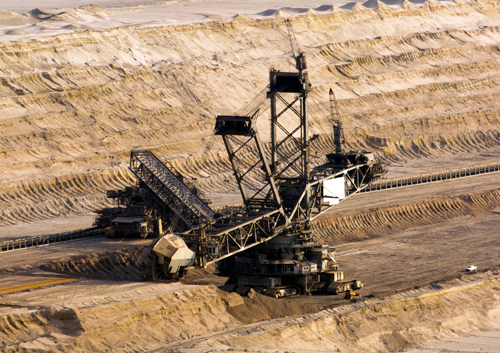
The mining industry is experiencing unprecedented change: to be successful, companies need to remain nimble and creative, yet focused on their goals. Now that is so obvious to most mining CEOs that it is almost a truism, yet in practice they need help. As mining companies move through the mining asset life cycle, they encounter different challenges to maintaining. Under its Global Head of Mining Wayne Jansen, KPMG’s experienced team of mining specialists, working from 13 mining centres in the world’s principal mining areas, assist clients daily and are developing innovative strategies so that they can get a clear, holistic picture of operations. One such solution is Data Analytics, which has found a limited footprint in the mining industry so far as a tool for operational excellence.
KPMG tends to use a combination of tools to achieve operational excellence, however when it first engages with a mine operation, according to Associate Director at KPMG in South Africa Harmeet Katari, the team will often adopt an approach that leverages tools built from the private equity market to quickly build and test hypothesis for cost optimisation. This is sustainable value improvement (SVI). “This way we can find out where the real value resides in the business, and pin down the cost drivers and the performance levers. Then when we get into the design and implementation phase we may bring in tools like lean, six sigma and analytics based solutions to some extent to bring about those changes.”
There is a place here for the process and value stream mapping techniques that manufacturing and process industries rely on, he adds. Frankly, lean took 40 years to become embedded in manufacturing, much more recently gained a foothold in the steel industry, and will take another couple of decades to be widely adapted and adopted in mining. It will take that long, Katari thinks, for the mindset to change – currently mining executives tend to solve business problems by spending capital rather than through efficiency programmes.
The adoption of analytics in mining is in its nascent stage. With huge amount of data being generated by the equipment in respects of its running condition, operating environment, performance, all of this information resides in different storage devices with companies not knowing how to use this data to make effective decision making. KPMG sees that the use of analytics in mining can be extensively used in asset management, integrated production planning, energy management, the supply chain, and to predict market demands.
Currently KPMG is helping its clients in two specific areas with very powerful solutions around integrated production planning and asset management, two of the biggest concern areas for any mining company.
Katari thinks that one of the biggest operating challenges mining companies face today is their ability to respond as a single unit when actual differs from plan. “I think this is a key area where companies fail; firstly by operating in organisation silos and secondly by not having the tools to re-optimise their plan and get over adverse events faster.” There are three parts to the mining value chain, he points out, pit operations, processing or beneficiation, and logistics – getting the product to the customer. These are the three organisational silos that too often fail to communicate effectively with each other.
The problem starts after the planning stages are complete, he says. Mining companies do an excellent job when it comes to creating life-of-mine plans, with a lot of effort to plan the ounces. The issues start when the plans are communicated to different functional units and that is when they start to operate in silos. “The mining people, the processing people and the logistics people work in their own ways. They communicate if there is a major event, a ship delay at the port or a derailment for example, but what we call small change events – day to day issues that crop up – are not reported. In my experience these events are daily, even hourly occurrences.”
But they do affect the plan. “How do I re-optimise my plan and change my target for the day or respond to a situation after a truck breakdown or a crusher stop?” This is the type of question that can be addressed through KPMG’s unique analytical solution, which takes different variables into a single solver and models different scenarios and creates a revised plan which is shared seamlessly across the organisation.
And it goes further. Lost blasts are typically caused by backlogs clogging up the mine, or by cleaning activity. Trains are often left waiting, either at the mine due to lost blasts, or delay at the processing plant as a result of full tips. A lack of ore can either cause a complete processor shutdown, or reduce yields due to inefficiencies. Costs rise, thanks to overtime for staff clearing backlogs and moving excess ore to temporary stockpiles, which also requires expensive equipment and transport. With these resources in constant use, maintenance suffers, leading to breakdowns or accidents.
KPMG’s Integrated Production Planning (IPP) solution, the objective of which is “Optimising as a single system on a dynamic basis with strong governance,” will start at the level of governance, because that is where the problem originates – nobody ‘owns’ the plan – so KPMG is working with many of its mining clients to improve the whole planning process to create integrated monthly, weekly and daily production schedules across the value chain. Use a strong optimisation engine which analyses the historical data and create a re-optimised plan and schedule for the business.
Asset management is another area where KPMG is assisting its clients through analytics. All large mining equipment has a multitude of data about its health being recorded on an ongoing basis. If used effectively, this data can help predict asset health. It is, Katari points out, like a human body wherein lots of internal and external means can help establish whether a particular part of the body is susceptible to breakdown and therefore preventive care can be taken. “Similarly, assets transmit different signals through real time data and operating conditions which can help in predicting the failure of an asset.”
Traditionally, mining companies follow a standard maintenance schedule as prescribed by the OEMs, which need not be optimal due to different operating conditions and also because of the inherent benefit which OEMs want to gain by replacing the parts before end-of-life. “The machines are forever talking but most of the time nobody is listening,” says Harmeet Katari: “Condition-based maintenance, or predictive analytics, is a key component under asset management.” KPMG has assisted its clients by developing tools which analyse the data and can predict when a component is likely to fail, allowing its replacement or service to be scheduled so as not to lose time. “A sound condition-based asset management strategy with strong analytical tools has helped our mining clients save at least ten to 15 percent of their costs, with another five to ten percent improvement in availability.”
While asset and production fleet management is easier to illustrate, many other areas benefit from the application of analytics as applied by KPMG. Productivity levels, yield management in processing operations, supply chain management and energy management all lend themselves to improvement through analytics. Warehousing and materials control is directly linked to understanding critical spares in the light of asset management standards while contractor and supplier performance management links directly to the way service contracts are formulated. Just as the operation needs to knock down its silos, co-ordinated scheduling of all the resources on a site, based on objective, targeted functions like profitability and asset utilisation allows the company to focus on net present value (NPV) rather than volume.
Analytics-based approaches are being taken on board by a growing number of clients, says Katari. “We can go in and use SVI at the diagnostic level, then we can help them identify those areas they can tackle on their own without external help. For the rest we believe we have the capability to partner with them and take them through that journey. And we engage with them at all levels, from top management to doing workshops with middle management and then going into the sites to explain in detail what needs to be done and how it will benefit the workers at the figurative, and literal, coalface.”
Words by John O’Hanlon, research by Richard Halfhide